In this post
Choosing methods of production
When making goods, a business can use several different processes to run efficiently and create things to the best standard. Each production method will have different advantages and disadvantages for the product that is being created so you should fully understand the best one for any situation.
Job production
The method of ‘job production’ is where a business makes one product from start to finish before it moves on to another. This means that one individual product is created at a time by a business and they are usually ‘one-offs’ or very high-end products.
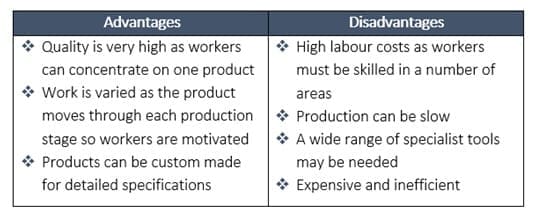
Batch production
As demand for products grows, a business may need to switch from job production to batch production. This still involves building a product from start to finish, but multiple products are created at once. A business may make a batch of 100 products that all pass through the stages of production at the same time. For example, a bakery will create a large amount of dough before splitting this into individual pieces. Each one will then be baked at the same time before they are removed from the oven and then cut into sliced loaves. This is an example of batch production as multiple products pass through the same stage at the same time.
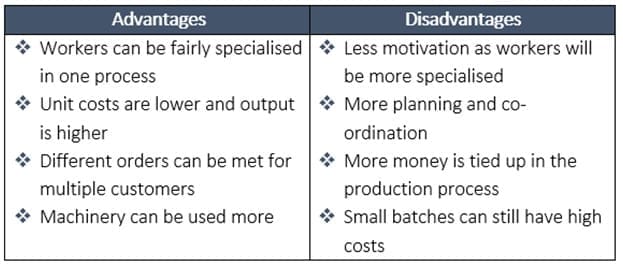
Flow production
A flow production is generally used when a business has a large number of products on sale and needs a steady stream of new products coming through. This type of production results in a lower cost per product to be paid and enables high levels of organisation, as well as specialist knowledge in each individual area of the process. Flow production allows a business to:
- Create large quantities of produce
- Make standardised products
- Employ a specialised workforce that are employed in one specific part of the production
- Use large amounts of machinery and integrate the latest technology into production processes
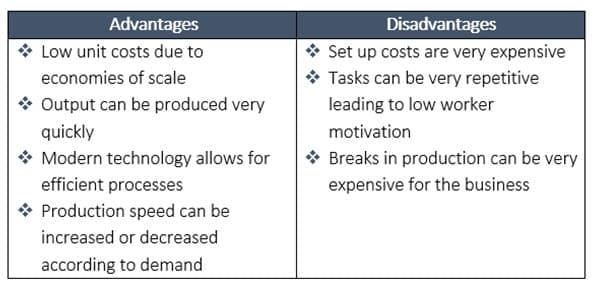
The impact of different production types
The different types of production that are used within a business will impact upon the profitability of goods that are on sale. Using a specific production method will result in differing levels of overall costs, costs per product made and production speed. Choosing a production method will require a business to understand the following:
- The type of product – products often require very specific types of production. For example, creating a toy in a factory will be done either in batch or flow production as building one individual toy at a time would be very inefficient. However, something like farming will have to be done through batch production due to the nature of products. The building of ships or other large items on the other hand will be done on a job production method as this is the only available way
- The size of the market – a market that is very large will have a constant demand that will need to be satisfied. This means that a business must have its products on sale all the time. Flow production is the only way to do this as it allows the business to have a steady number of products that are created every day. For example, a company that manufactures food products will need to use flow production as this will allow the business to stock shops all of the time to meet a demand that does not go away
- The stage of the business – when a firm first starts it is likely to have low levels of cash. This means that a cheaper production method should be used. Although flow production may be the first choice for cheap production (which is true for cost per product), it is actually very expensive to set up. Usually, it requires high levels of staff, materials and expensive assembly lines. The cheapest method of production for a small firm that is growing would be job production as cash will not be tied up in materials used in the manufacturing process. As a business gets larger and can invest profits in more products and equipment, it may move to batch or flow production in order to reduce the cost of each item being made
When a business grows and the assets that it has are increased it can benefit from investing back into production processes. Once this happens, efficient processes can be implemented into the business in order to keep productivity high and costs low. Doing this will help a company to offer products at a lower price than its competitors –something that will increase competition in the market.